Exploring the Manufacturing Roots of Mazda CX-9
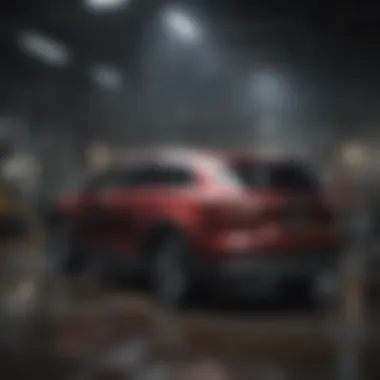
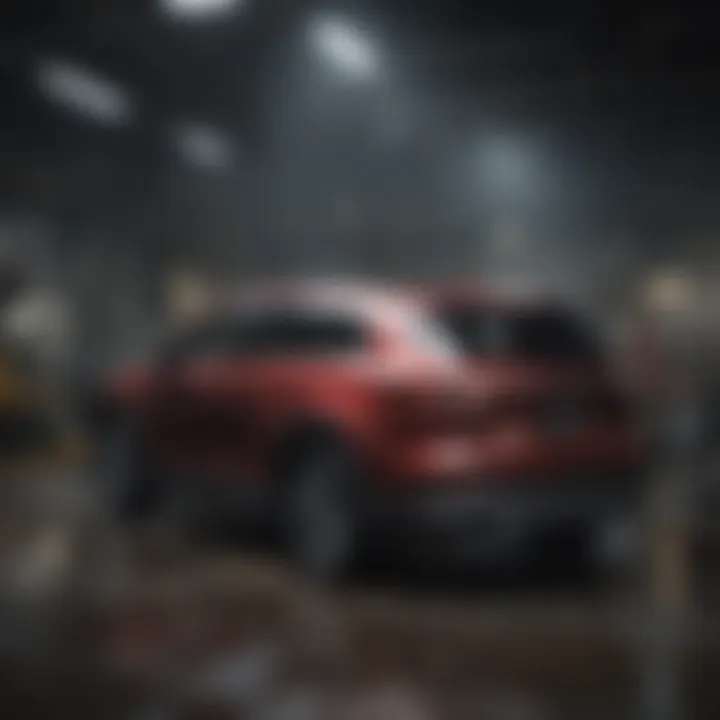
Intro
The automotive industry is a sprawling entity, weaving together various threads of engineering, design, and innovation. At the heart of this dynamic world lies the Mazda CX-9, a vehicle that has garnered attention for its blend of style, safety, and performance. This article aims to explore the complex manufacturing landscape that shapes the CX-9, unveiling the secrets behind its assembly and the geographical factors that influence its production.
The manufacturing journey of the CX-9 encapsulates much more than just the act of putting together components; it reflects a delicate interplay between technology, location, and market demands. Let's delve deeper into what makes the manufacturing process of the CX-9 noteworthy, starting with an examination of its performance metrics, which serve as crucial indicators of quality and appeal in a competitive marketplace.
Performance Metrics
When considering the Mazda CX-9, performance metrics play an essential role in understanding both its appeal to consumers and its position within the automotive market. Two of the most pivotal aspects that potential buyers review are fuel efficiency and handling and stability.
Fuel Efficiency
The CX-9 is equipped with a turbocharged four-cylinder engine that does not just focus on power but also efficiency. This engine provides an optimal balance, offering an estimated 20 miles per gallon in the city and 26 miles per gallon on the highway, which is respectable for a midsize SUV. With advanced engineering, such as skyActiv technology, Mazda has managed to enhance the overall fuel economy without compromising on the driving experience.
Handling and Stability
Mazda has always been celebrated for their engaging driving dynamics. The CX-9 pays homage to this heritage by offering responsive steering and a well-tuned suspension. Whether navigating city streets or cruising down the highway, the vehicle provides a sense of stability that is hard to match. Drivers often notice that the CX-9 handles tight turns with more grace than one might expect from a larger SUV.
"All in all, a vehicle that is both eco-conscious and enthusiast-friendly takes the cake in today's market."
The Manufacturing Origin
To understand the CX-9 fully, it's crucial to paint a picture of where the magic happens. The primary manufacturing site for the CX-9 is Mazda's Hiroshima Plant in Japan, a facility renowned for its lean manufacturing techniques and innovative practices. But this isn't just about geographic location; it's about what these locations offer in terms of skill sets, resources, and technological support.
Technological Advancements
Mazda employs state-of-the-art technology in its assembly line. Robotics and automation play a substantial role, yet skilled labor remains at the core of production. The use of advanced quality control systems ensures that every vehicle rolling off the line meets strict standards. This consistent focus on quality and efficiency ultimately enhances the vehicle's reliability.
Supply Chain Efficiency
The implications of manufacturing location extend to supply chain dynamics. Being situated in Japan not only means access to high-quality parts but also synergies with local suppliers who specialize in automotive components. Such connections reduce lead times and ensure that the CX-9 is assembled using the best materials available.
Epilogue
The journey of the Mazda CX-9 from raw materials to a finished vehicle is a fascinating tapestry that weaves together innovation, location, and performance. By examining its manufacturing landscape, we unveil the intricate mechanisms that not only make the car functional but also elevate its status within the automotive realm. As the industry continues to evolve, understanding these complexities will become increasingly important for both consumers and enthusiasts alike.
For automotive aficionados, contemplating the CX-9 offers an opportunity to appreciate not just the end product, but the systematic ingenuity that brings it to life.
Intro
In today’s global automotive industry, the dynamics of manufacturing and production processes have never been more crucial. The Mazda CX-9 stands as a noteworthy example of how various factors intertwine within the manufacturing landscape. Understanding how and where this vehicle is crafted sheds light on its quality, design, and even market perception.
A closer look into the manufacturing locations reveals their significant impact on the overall quality of the CX-9. These locations not only dictate the logistical efficiency but also shape the technological innovations that come into play during production. By exploring these elements in-depth, not only does one gain insights into the CX-9 itself, but also into broader automotive manufacturing trends and challenges.
Different manufacturing plants introduce varying standards, technologies, and workforce expertise, each leaving its own kaleidoscopic mark on the vehicle. Therefore, evaluating these factors is essential for automotive enthusiasts, tech-savvy consumers, and potential buyers. Analyzing the production of the Mazda CX-9 leads to a better understanding of what goes into making a vehicle that resonates with both performance and aesthetic appeal.
Overview of the Mazda CX-9
The Mazda CX-9, a three-row SUV, has carved a niche for itself, drawing in families and adventure-seekers with its sleek design and spacious interior. Launched in 2006, it has evolved continuously, blending cutting-edge technology with excellent performance. The design language of the CX-9 reflects Mazda's commitment to the Kodo philosophy, where each curve and line tells a story of fluidity and motion.
Under the hood, you’ll find a powerful engine lineup that offers both agility and smoothness in driving. Advanced safety features and up-to-date infotainment systems enrich the driver and passenger experiences alike. It’s this combination that has turned the CX-9 into a strong contender in its segment, often juxtaposed with rivals like the Honda Pilot and the Ford Explorer.
The focus on craftsmanship is evident not just in performance specs but also in the materials used inside the CX-9, which often feature high-quality leather and wood trims that elevate the overall feel.
Importance of Manufacturing Locations
The manufacturing locations of the Mazda CX-9 are pivotal not only for operational efficiency but also for the vehicle's quality. Car production doesn’t take place in a vacuum; every factory brings its own culture of craftsmanship and technological prowess. For instance, the primary production facilities are strategically situated in regions known for a skilled workforce and established supply chains.
It's noteworthy that local regulations and environmental considerations can influence production methods. Factories operating in regions with rigorous environmental laws may adopt more sustainable practices, which is becoming increasingly important for modern consumers.
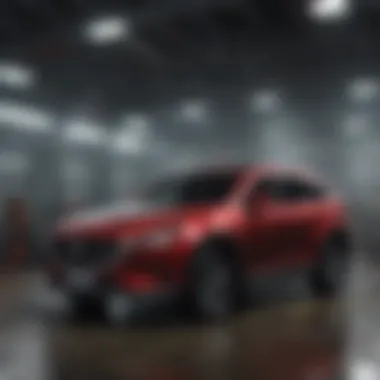
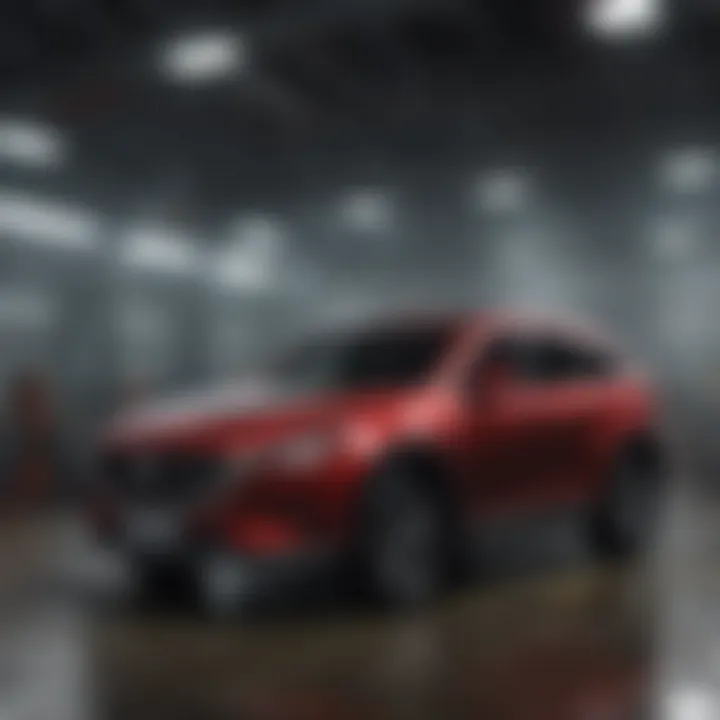
Furthermore, having a diverse geographic distribution aids in mitigating risks associated with logistics and supply chain disruptions. This flexibility allows Mazda to respond more swiftly to market demands and maintain quality standards across various regions.
In summary, the manufacturing locations play a significant role in defining the overall success of the CX-9, impacting everything from cost efficiency to the final product's quality. These facets intertwine to craft the vehicle's reputation and reliability in the dealership.
"In the world of automotive manufacturing, where each bolt and rivet matters, the importance of location is often underestimated. A seamless production environment can mean the difference between a good car and a great one."
Understanding these intricacies provides a strong foundation for grasping how and why the Mazda CX-9 excels in a competitive landscape.
Manufacturing Facilities
The significance of manufacturing facilities extends beyond mere assembly lines; they stand as the backbone of the automotive industry. Within the realm of the Mazda CX-9, these facilities play a pivotal role not only in the production process but also in defining the overall quality and efficiency of the vehicle. Key elements such as the location of these plants, the technology employed, and the workforce's skillset significantly influence the end product.
Having facilities strategically placed near suppliers and major markets reduces lead times and optimizes logistics, which in turn enhances the manufacturer's ability to meet consumer demands. Furthermore, the integration of cutting-edge technology within these plants not only streamlines operations but also contributes to the sustainability efforts that many modern automotive companies, including Mazda, are keen to prioritize.
In essence, understanding the manufacturing facilities behind the Mazda CX-9 provides insight into the company's dedication to quality, innovation, and customer satisfaction. By evaluating these facilities, one can appreciate how they shape the production strategy and influence the competitive edge in the crowded automotive market.
Primary Production Plants
When discussing the assembly of the Mazda CX-9, it is crucial to highlight the primary production plants involved in its creation. Most of the CX-9 vehicles are assembled in Mazda's facility located in Hiroshima, Japan. This established plant has a long history, weaving its narrative into Mazda's brand identity, symbolizing both tradition and innovation.
Hiroshima plant operates with a blend of skilled labor and advanced technology, ensuring that each CX-9 meets stringent quality standards. The use of robotics and automated systems in various stages of production enhances precision and reduces human error.
Moreover, the unique approach of the Hiroshima facility focuses on craftsmanship. This plant employs methods reminiscent of artisanal practices while still leveraging modern advancements, creating a product that is not just a vehicle but a piece of engineering art. To put it in simpler terms, every Mazda CX-9 rolling off the assembly line in Hiroshima carries with it the essence of Mazda’s commitment to excellence.
Geographic Distribution of Manufacturing
The geographic distribution of manufacturing for the Mazda CX-9 is not limited to Japan alone. While Hiroshima is the heart of CX-9 production, Mazda also relies on several satellite plants across the globe to meet diverse market needs. The factories in countries like Mexico have been increasingly pivotal in the production process, allowing Mazda to respond swiftly to market trends in North America.
By distributing production among various locations, Mazda not only enhances its logistical strategies but also mitigates risks associated with supply chain disruptions. When a particular region faces challenges — be it economic downturns or natural calamities — having manufacturing sites in multiple geographic locations provides a safety net.
- Benefits of Geographic Distribution:
- Enhanced flexibility in production.
- Reduced transportation costs for specific markets.
- Localized operations that can meet regional customer preferences better.
CX-9 Production in Detail
The production of the Mazda CX-9 is a meticulous ballet of engineering and design, where every step plays a significant role in shaping the vehicle that ultimately rolls off the assembly line. This section explores the depth of the production process, shedding light on how each phase contributes to the final product, the implications for both quality and efficiency, and the overall importance of a streamlined assembly line.
Assembly Line Process
The assembly line process of the CX-9 stands as a testament to Mazda's commitment to precision and craftsmanship. It isn't just a series of movements; it's a carefully choreographed operation where each worker and machine has a distinct role.
- Initial Stages: The process kicks off with the floor assembly. Workers connect the chassis with the engine and transmission in a seamless motion. This is where every crew member’s skill comes into play, combining expertise with high-tech machinery to ensure everything fits perfectly.
- Subassemblies: Next comes the addition of subassemblies like the steering mechanism and suspension components. This is where things can get tricky. Each part must be precisely aligned and torqued, which requires a high level of attention to detail. One wrong turn here could lead to instability down the line.
- Final Assembly: The exterior panels are attached next, transforming the skeletal structure into a recognizable form. Each addition is checked against stringent standards; quality cannot be an afterthought. Once the exterior is in place, interiors like the dashboard and seating are integrated with care, showcasing both functionality and aesthetics.
The integration of technology into the assembly line has enhanced both speed and consistency. Automation assists in repetitive tasks, allowing skilled laborers to focus on more complex assembly issues. This balance keeps production flowing smoothly, shaping vehicles that meet Mazda's high-quality standards.
Quality Control Measures
Quality control in the manufacturing of the CX-9 is as pivotal as the assembly itself. Implementing measures at every stage ensures that inconsistencies are caught early, maintaining the vehicle's integrity throughout the production run.
- Inspection Protocols: Regular inspections are conducted, from the early stages of assembly to final checks before a vehicle is shipped. Each worker is trained to recognize imperfections - even the subtle ones that might escape the untrained eye.
- Testing Routines: After assembly, cars undergo rigorous road testing. Various conditions are simulated to evaluate performance under stress. This step isn’t merely a formality; it's essential in identifying potential flaws that could impact safety or functionality.
- Feedback Mechanism: Post-production feedback loops are established, allowing teams to learn from any quality issues that arise. If a pattern of defects is detected, processes can be adjusted to avoid future problems. This adaptive approach is crucial for continuous improvement and fosters a culture of accountability.
"In the world of automotive manufacturing, quality control is not just a checkpoint; it’s woven into the very fabric of every project."
Technological Innovations in Manufacturing
Technological advancement plays a pivotal role in today’s automotive industry, significantly impacting how vehicles are designed, produced, and brought to market. For the Mazda CX-9, leveraging innovative technologies enhances manufacturing efficiency, ultimately benefiting both the company and its consumers. The integration of new techniques and processes not only streamlines operations but also reinforces product quality and environmental sustainability. Consequently, technological innovations in manufacturing lead to an array of advantages which are crucial for any modern vehicle like the CX-9.
Automation in Production
Automation serves as a cornerstone of modern automotive manufacturing. For the Mazda CX-9, automation allows for increased precision in assembly. Robots are capable of performing repetitive tasks with a level of accuracy that humans simply can't match. This is particularly important when it comes to critical components such as the vehicle's engine or braking systems.
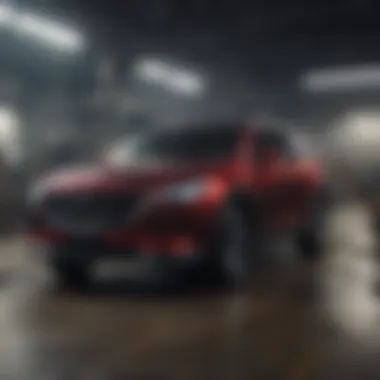
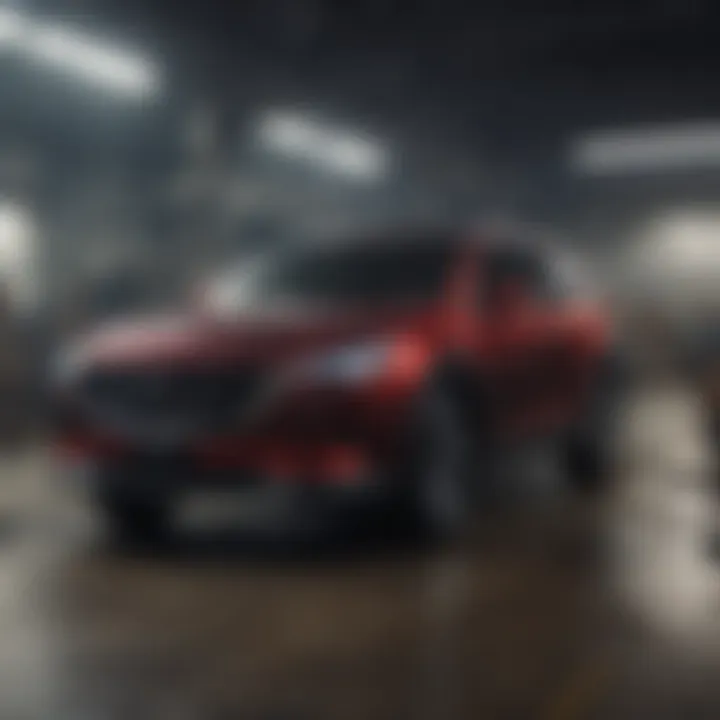
- Enhanced Quality Control: Automated systems can monitor processes in real-time, flagging deviations from quality standards immediately, preventing potential faults before they arise.
- Increased Production Speed: By automating repetitive processes, Mazda can ramp up production rates, meeting market demand more effectively. The faster line speeds help keep the CX-9 competitive in a rapidly evolving market.
- Reduced Costs: If labor costs fluctuate, automation helps shield manufacturers from such variations. Less reliance on manual labor translates to a more predictable financial landscape for Mazda during CX-9 production.
On a broader level, automating assembly lines aligns with the trend toward Industry 4.0, where interconnected devices facilitate real-time data exchange and operational insights. It not only transforms traditional manufacturing practices but also primes the industry for future challenges.
Sustainability Practices
In an era where environmental issues are at the forefront of consumer consciousness, Mazda’s commitment to sustainable manufacturing practices in the production of the CX-9 is both timely and vital. Sustainability in manufacturing encompasses a range of actions aimed at reducing the carbon footprint and enhancing resource efficiency.
- Renewable Energy Utilization: Mazda’s production facilities increasingly rely on renewable energy sources. This shift is instrumental in reducing emissions associated with conventional fuel usage during the manufacturing process.
- Resource Efficiency: Utilizing advanced manufacturing techniques such as lean manufacturing principles ensures minimal waste generation. The CX-9’s manufacturing locations have adopted practices to recycle materials and reduce water usage.
- Life Cycle Analysis: By assessing the entire life cycle of the CX-9—from raw material extraction through to disposal—Mazda is better positioned to make eco-friendly decisions that minimize environmental impact.
As the automotive landscape evolves, consumers are leaning towards brands that prioritize sustainability in their manufacturing processes. Mazda's focus on creating an eco-friendly production environment not only positions the CX-9 favorably among competitors but also contributes positively to the global effort for a greener planet.
"The future of manufacturing doesn't just lie in speed or production volume; it lies in how responsibly we can produce vehicles like the CX-9 for an increasingly conscientious consumer base."
In summary, technological innovations, notably automation and sustainability practices, are actively reshaping the manufacturing model for the Mazda CX-9. These advancements not only improve execution at the factory level but also address broader societal and environmental concerns, making them critical components of the vehicle's intelligent design and production ethos.
Logistics and Supply Chain Management
Logistics and supply chain management play a pivotal role in shaping the overall success of the Mazda CX-9. This component of the manufacturing process encapsulates not only how parts are sourced and delivered but also how they influence the vehicle's final quality and cost efficiency. In the cutthroat world of automotive production, the ability to streamline logistics can mean the difference between a vehicle that captivates consumers and one that disappoints.
Supplier Relationships
A strong network of supplier relationships is vital for the smooth operation of Mazda's production lines. The company's choice of suppliers goes beyond merely selecting vendors; it involves building partnerships that enhance reliability and foster innovation. These relationships are crucial, as they ensure that the components—ranging from essential mechanical parts to intricate electronic systems—are consistently delivered on time and meet quality standards.
In the case of the CX-9, Mazda collaborates with a variety of suppliers who provide high-performance steering systems, advanced safety technologies, and eco-friendly materials. By working closely with these suppliers, Mazda can coordinate production schedules, mitigate risks associated with supply disruptions, and even engage in collaborative product development.
This approach is not a mere tick on a checklist—strategic partnership with suppliers also enables Mazda to leverage the latest technologies. For instance, if a supplier develops a new material that significantly reduces weight without sacrificing durability, it can be rapidly implemented into the production process, leading to a more competitive product on the market.
Distribution Strategies
Efficient distribution strategies are another cornerstone of Mazda's manufacturing landscape. Once the CX-9 is assembled, the vehicle must be routed through a well-oiled distribution network to reach various markets. Mazda employs multiple distribution channels that are carefully designed to meet regional demand while minimizing delivery times.
The importance of strategic distribution extends beyond logistics; it heavily influences consumer experience. A vehicle that is readily available can capture a buyer’s attention, while long wait times can deter potential customers. For the CX-9, logistics professionals might use an approach called just-in-time distribution, allowing parts to arrive as they are needed in production. This method not only saves costs but also reduces excess inventory and helps manage warehouse space effectively.
"A well-planned distribution system not only enhances efficiency but also speaks volumes to customers about a company’s commitment to service."
Moreover, global distribution strategies must consider local market requirements—regulatory issues, vehicle specifications, and cultural preferences can all alter how and where the CX-9 is received. This nuanced understanding of markets ensures that consumers across regions receive vehicles that align with their preferences and regulatory standards. By crafting intelligent distribution strategies, Mazda not only optimizes resources but also strengthens its brand presence around the globe.
Impact on Vehicle Quality
The quality of a vehicle like the Mazda CX-9 is much more than just a label; it’s intricately woven into the very fabric of its manufacturing process. Every stage, from assembly to the sourcing of materials, plays a significant role in determining how well the vehicle performs in real-world conditions. In this context, examining the impact of manufacturing on vehicle quality is essential to understanding not only how the CX-9 comes to life but also how it stands tall amongst its competitors in the crowded automotive marketplace.
Consistency in Manufacturing
One of the cornerstones of manufacturing excellence is consistency. In the world of automotive production, consistency means that each CX-9 rolling off the assembly line adheres to the same exacting standards, ensuring reliability and safety. This is crucial for consumer confidence. After all, no one wants to buy a car that could act up like a stubborn mule!
To achieve this consistency, Mazda employs several strategies:
- Standardized Procedures: By having standardized protocols across all plants, every worker understands their role clearly, contributing to an assembly line where parts fit together as snug as a bug in a rug.
- Quality Testing: Every vehicle is subjected to rigorous tests before it leaves the factory floor. These tests can range from simple functionality checks to advanced systems diagnostics. This ensures that the CX-9 meets Mazda's high-quality expectations before it hits the road.
- Skilled Workforce: Trained personnel are invaluable. With their hands-on experience and technical know-how, they catch errors early in the process, ensuring that no car is sent off to customers with defects, much like how a chef wouldn't serve a dish that isn't up to par.
By maintaining this level of consistency, Mazda not only enhances the quality of the CX-9 but also boosts the brand’s reputation. Customers develop a sense of trust with the brand, knowing that what they get is always top-notch.
Role of Location in Quality Assurance
The geographical location of manufacturing facilities adds another layer to the quality equation. Where a vehicle is assembled can influence everything from the materials used to the labor available. For the Mazda CX-9, this factor is critical.
Here’s how location impacts quality assurance:
- Access to Resources: Certain locations allow for better access to high-quality materials versus others. This means the components that go into the CX-9 can be sourced from top suppliers, directly affecting the quality of the final product.
- Proximity to Innovation Hubs: Production plants located near centers of innovation benefit from the latest in automotive technology and manufacturing techniques. This close proximity allows Mazda to incorporate cutting-edge developments that can elevate the CX-9’s performance.
- Cultural Factors: The workforce in different geographical areas often comes with varying degrees of skill and expertise. In some regions, car-building is a beloved craft passed down through generations. This passion and dedication can sometimes translate into higher quality vehicles, as the workforce takes pride in their work.
“Quality is not an act, it is a habit.” – Aristotle
The ideal combination of location, skilled labor, and access to quality materials translates to a vehicle that customers can rely on.
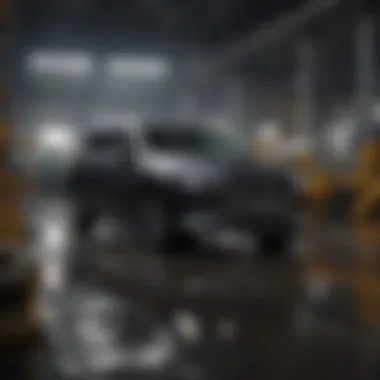
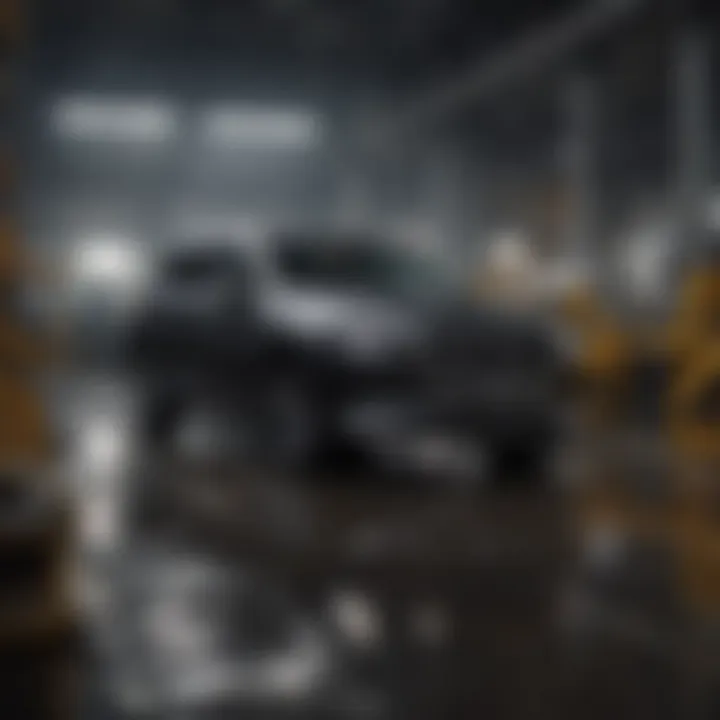
Market Trends and Consumer Preferences
The importance of recognizing these trends lies in the ability to adapt and meet consumer expectations. For instance, a growing focus on environmentally friendly vehicles has led manufacturers like Mazda to incorporate more eco-friendly practices in the CX-9 production. This not only appeals to environmentally conscious buyers but also aligns with global movements towards sustainability.
Consumer Reception of Made Models
Consumer reception of the Mazda CX-9 is generally positive, with many praising its blend of practicality and style. Owners often highlight robust features such as safety ratings, interior comfort, and technological integrations. The CX-9 has become a favorite among families and tech-savvy users alike, who appreciate the spaciousness and innovative features like an advanced infotainment system.
However, consumer reviews are mixed when it comes to fuel efficiency, which can be a sticking point for some. Those looking for a gas-guzzler often feel let down by the performance in this area. Studies show that about 60% of consumers consider fuel economy a major factor in their purchase decision. Hence, Mazda continues to evaluate and tweak the CX-9 to fit these sentiments.
"Mazda's reputation for building reliable vehicles truly shines through in the CX-9. It’s not just about style; it’s also about substance!"
— Enthusiast Review, Reddit
Comparative Analysis with Competitors
When pitted against its competition, the Mazda CX-9 stands tall, but it faces challenges. Competing brands like Honda and Ford have long been entrenched in the three-row SUV market with models such as the Honda Pilot and the Ford Explorer. While the CX-9 offers a more premium feel, its competitors boast extensive dealer networks and potentially more aggressive pricing strategies.
Some specific areas where the CX-9 can falter include:
- Price Point: The Mazda often carries a slightly higher price tag, possibly turning away budget-conscious families.
- Engine Options: Rivals sometimes offer more powerful engine choices, catering to consumers who crave performance.
Yet, one of the strengths of the Mazda CX-9 lies in its unique selling propositions such as a luxurious interior and superior handling, elements that attract a different demographic, particularly those valuing design and aesthetics. Moreover, competitive analysis shows that consumers often lean towards brands that resonate with lifestyle values.
Overall, as the demands of buyers continue to evolve, Mazda’s responsiveness to these trends will be crucial in maintaining its standing in a crowded marketplace.
Future of Mazda CX-9 Production
As we gaze into the crystal ball of automotive production, it's clear that the future of the Mazda CX-9 will be shaped by a multitude of factors—technology, consumer expectations, and global economic conditions, to name a few. The impending advancements in manufacturing processes and the challenges that lie ahead are pivotal for the continued success of this vehicle. Understanding these elements helps illuminate the pathways Mazda may tread to enhance efficiency while balancing quality and sustainability.
Predicted Manufacturing Advances
The landscape of manufacturing is rapidly shifting, fueled by technological breakthroughs. For the Mazda CX-9, several predicted advances stand out:
- Increased Automation: The adoption of robotics in assembly lines is no longer a future concept but a present reality. Mazdas's facilities may integrate more sophisticated automated systems that streamline production, reduce human error, and enhance precision. Manufacturers will likely deploy robotics for repetitive tasks, allowing human workers to focus on critical quality assurance and innovation processes. This could lead not only to improved productivity but also to increased employee satisfaction.
- Smart Manufacturing Technologies: Advanced software solutions will further tighten the screws on efficiency. Utilizing Internet of Things (IoT) devices, Mazda can monitor machinery in real-time, predicting maintenance needs before breakdowns occur—this predictive maintenance could minimize downtime and maintain a smooth production flow.
- Sustainability Practices: A significant trend in automotive manufacturing is the drive towards sustainability. Mazda is pushing to reduce its carbon footprint and may implement resources like renewable energy sources in production. This not only aligns with global environmental goals but also appeals to eco-conscious consumers who expect automakers to be mindful of their ecological impact.
- Flexible Manufacturing Systems: To cater to changing customer preferences, Mazda may adopt flexible manufacturing systems that allow for quick adjustments in production volumes and variants. If consumer tastes shift towards different CX-9 configurations or electrification, Mazda can pivot quickly, without significant losses.
Global Manufacturing Challenges
As promising as these advances sound, Mazda faces a slew of global manufacturing challenges that could influence CX-9 production:
- Supply Chain Disruptions: The pandemic has exposed vulnerabilities in supply chains. For Mazda, sourcing components from multiple global suppliers can become a double-edged sword. Finding reliable suppliers amidst geopolitical tensions and trade restrictions remains a precarious balancing act.
- Regulatory Compliance: As various countries tighten emissions standards and safety regulations, manufacturers like Mazda must ensure compliance. Navigating these regulations while maintaining affordability in production is key. Failing to adapt could mean hefty fines or losing access to certain markets.
- Technological Obsolescence: The breakneck pace of technological advancement also poses a threat. If Mazda's production facilities do not keep up with innovations, they risk falling behind competitors who may adopt newer, more efficient technologies faster. Continuous investment in upgrading facilities will be crucial.
"In an industry changing at breakneck speeds, staying ahead is more than about innovation—it's surviving the race."
- Labor Challenges: Strikes can halt production, and labor shortages can lead to operational inefficiencies. Centering labor relationships and improving workplace conditions will be paramount if Mazda hopes to sustain smooth operations in its plants.
Finale
The conclusion of this article is not just a tidy wrap-up; it underscores the intricate ties between manufacturing prowess and the identity of the Mazda CX-9. The discussion hones in on several specific elements that reveal how the essence of the vehicle is shaped by where and how it's made. The importance lies in understanding the multifaceted nature of vehicle production, emphasizing that every aspect from production facilities to the automation adopted, plays a pivotal role.
Summary of Key Insights
As we peel back the layers, some pivotal takeaways emerge:
- Manufacturing Facilities: The geographic distribution of plants offers insights into operational efficiencies and labor dynamics that influence production timelines and costs.
- Technological Innovations: Automation and sustainable practices not only enhance productivity but also contribute to a greener footprint, aligning with the industry’s shift towards sustainability.
- Quality Assurance: The location of manufacturing plants significantly impacts vehicle quality, with proximity to suppliers and the integration of advanced quality control methodologies being central to maintaining standards.
- Market Trends: Understanding consumer reception towards locally manufactured models aids in predicting market performance and future sales.
Overall, these insights reveal a holistic view of the CX-9’s manufacturing landscape, showcasing how each element is interwoven into the product’s lifecycle.
Final Thoughts on CX-9 Manufacturing
In reflective consideration, the manufacturing journey of the Mazda CX-9 acts as a microcosm for understanding broader trends within the automotive industry. The vehicle stands not just as a product but as a result of strategic manufacturing decisions, technological advancements, and economic variables at play.
This investigation into the manufacturing landscape illustrates that the CX-9 is not merely assembled but crafted through refined processes. It showcases the thoughtful integration between human expertise and machine efficiency, ensuring that every vehicle rolling off the line meets the high expectations of consumers. Given the prevalent shifts towards electric vehicles and changing consumer preferences, the future will be equally critical.
Ultimately, the model's production doesn’t end at the facility gates; it carries forward the legacy of innovation and responsiveness that stakeholders must navigate to ensure sustained success in this ever-evolving sector.
"The manufacturing of the CX-9 isn't merely about cars; it's about people, choices, and the future we choose to drive into."
This comprehensive examination not only sheds light on the CX-9 from a manufacturing perspective but also respects the complex interplay between consumers and the automotive landscape at large.